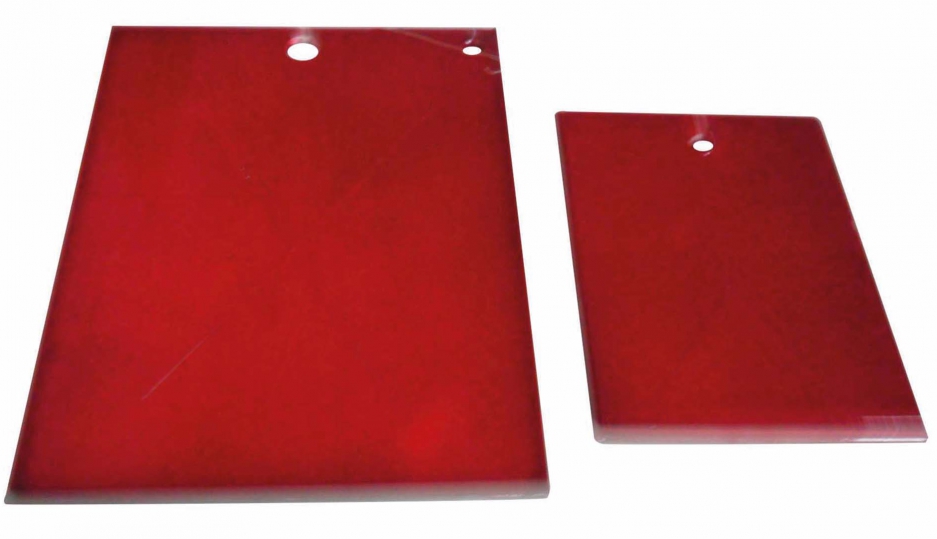
Sete processos, e suas fórmulas, de modo comparado para escolher aquele que melhor se adequa às suas necessidades
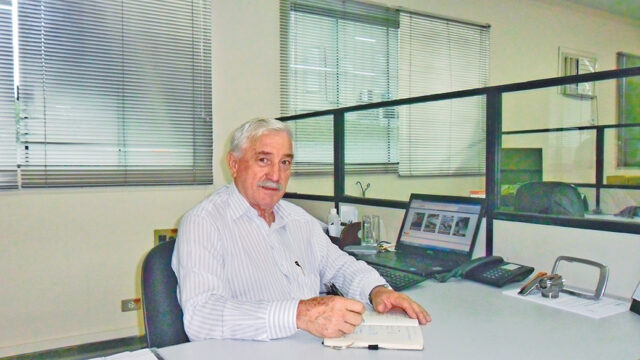
Diretor de processos quÃmicos da Alpha Galvano QuÃmica
jose.carlos@alphagalvano.com.br
O alumÃnio é um dos metais mais abundantes na crosta terrestre e, devido à s suas propriedades – baixo peso (densidade 2,75 g/cm³); três vezes mais leve que o ferro (7,87 g/cm³); boa condutividade elétrica; resistência à corrosão; e baixo ponto de fusão – propicia uma multiplicidade de aplicações, principalmente na indústria aeronáutica e automobilÃstica.
Sua fácil conformabilidade e resistência à corrosão faz com que ele, quando bem preparado, tenha grande aplicação na indústria da construção civil.
Durante o século 20, o alumÃnio teve uma grande evolução, com a produção mundial reportada de 6.800 toneladas em 1900 para 1.490.000 toneladas em 1950! E, durante a década de 1950, ultrapassou a produção do cobre, tornando-se o metal mais produzido no mundo, com a produção atual estando próxima a 60 milhões de toneladas por ano.
Com o aumento de produção e aplicações, a necessidade de tratamento do alumÃnio começou a ganhar proporção na década de 1950, e os primeiros processos de tratamento de conversão de camada a serem utilizados eram baseados em soluções ácidas ou alcalinas de cromo hexavalente.
Processo alcalino operando acima de 80°C, em soluções contendo 2 a 3% de soda e 0,5 de bicromato de potássio, com 10 a 20 minutos de imersão, deixando uma camada cinza porosa de 1,0 a 2,5 microns de espessura, composta de óxidos de alumÃnio com sais de cromo dispersos que podiam ganhar maior proteção, selando em solução de bicromato de potássio 5% aquecida.
Esses processos foram sendo substituÃdos pelos processos ácidos com cromo hexavalente, com real redução no consumo de energia, conseguindo acabamento amarelo iridescente tanto mais escuro quanto maior a espessura do filme formado. Eram soluções contendo fluoretos, responsáveis pelo ataque ao alumÃnio, passando o alumÃnio metal para Ãon de alumÃnio na solução conforme segue:
2 Al° - 6 e- ?  2 Al+3
Os elétrons são cedidos pela acidez da solução:
6 H+ + 6 e- ? 3 H2
O hidrogênio formado irá reagir com o ácido crômico, contido na solução, formando o hidróxido de cromo:
H2Cr2O7 + 3 H2Â ? Â Â 2 Cr (OH)3 + H2O
O ácido crômico foi adicionado à solução como trióxido de cromo que, ao reagir com a água, forma o ácido crômico:
2 CrO3 + H2OÂ ? Â Â H2Cr2O7
Assim sendo, na interface da reação, estarão presentes cromo na forma trivalente Cr(OH)3 (hidróxido de cromo) e na forma hexavalente CrO4-2 (cromato), responsáveis pela formação do composto presente no filme formado:
2 Cr(OH)3 + CrO4 -2 + 2 H+ Â ? Â Â Cr(OH)3 Cr(OH)Cr)3 + H2O
No filme também está presente o óxido de alumÃnio formado:
2 Al+3 + 6 OH- ? Â Al2O3 + 3 H2O
Ele completa o filme coloidal formado na forma gelatinosa – e fácil de ser danificado pelo toque, ficando mais firme após a secagem:
Al2O3Cr(OH)3Cr(OH)CrO3
Para um filme mais consistente também é introduzido na fórmula o ferrocianeto de potássio, formando um filme de ótima aparência, inclusive sendo utilizado como acabamento final decorativo:
CrFe (CN)6 Cr (OH)3 H2 Cr O4 4Al2O3 8H2O
Novas fórmulas
Outra grande mudança no pré-tratamento do alumÃnio foi a introdução da fosfocromatização que, junto com os cromatos, agrega ácido fosfórico, que pode também conter nÃquel na formulação. Basicamente, o filme formado é de CrPO4AlPO4H2O com, aproximadamente, CrPO4 (50 – 55%), fosfato de cromo, AlPO4 (17 – 23 %), fosfato de alumÃnio e H2O (22 – 23%), água.
Esse acabamento, contendo cromato e fosfato, tem excelente resistência à corrosão, inclusive atende as normas militares americanas. E, embora não contenha cromo hexavalente no filme formado, a solução é base cromo hexavalente, expondo os operadores ao risco e problemática ao meio ambiente.
Uma alternativa foi o uso de processos de base cromo trivalente formulados com produtos base fluoreto de cromo e ácido hexafluorzircônio, resultando em finas camadas de cromo trivalente dopadas de zircônio, conferindo boa resistência à corrosão, boa aderência de tinta, com processos que atendem as necessidades, porém, embora na forma trivalente, ainda contêm cromo na formulação, transferindo o problema do manuseio de cromo hexavalente para o formulador de produtos que, para a preparação dos produtos, inicia com uma reação de redução do cromo hexavalente CrO3 (trióxido de cromo) ou K2Cr2O7 (bicromato de potássio) ou Na2Cr2O7 (Bicromato de sódio).
Finalmente uma solução atóxica
O resultado isento de cromo, com resultado satisfatório de boa resistência à corrosão e aderência da tinta, foi obtido com a utilização de fosfato de zinco. O seguinte mecanismo de reação está envolvido na formação da camada de fosfato de zinco sobre a superfÃcie do alumÃnio.
O ácido fosfórico junto com o óxido de zinco formam o fosfato de zinco, podendo se apresentar nas formas primária Zn(H2PO4)2, secundária ZnHPO4 e terciária Zn3 (PO4)2, sendo que a forma primária é solúvel em água, a secundária é ligeiramente solúvel e a terciária é insolúvel.
Na solução está presente a forma primária Zn(H2PO4)2.
A primeira reação, será o ataque ao alumÃnio:
2Al ? Â 2Al3+ + 6 e-
Esses elétrons reagem com ions H+ reduzindo o pH na interface de reação:
6 H+ + 6 e- ? Â H2
Esse hidrogênio é extraÃdo do fosfato de zinco primário Zn (H2PO4)2, formando fosfato de zinco terciário Zn3(PO4)2 que, por ser insolúvel, precipita sobre a superfÃcie, formando cristais com ótima aderência.
A reação secundária gerada na solução está relacionada com o alumÃnio que foi dissolvido no ataque, reagirá parte dele com o ácido fosfórico e parte com o flúor da solução, formando fosfato de alumÃnio e fluoreto de alumÃnio:
Al3+ + PO43- ? Â AlPO4 e Al3+ + 6 F- ? AlF63-
Eles reagem com o sódio contido na solução formando hexafluoraluminato de sódio:
AlF63- + 3 Na+ ? Â Na3AlF6 ?
que precipita formando lama no banho, principal problema do processo de fosfatização de alumÃnio.
É de suma importância que a concentração de flúor na solução esteja bem balanceada. Se a concentração for baixa, o ataque será minimizado e a formação de filme pode não ser suficiente para conferir a proteção adequada. Já se a concentração estiver além do necessário, irá elevar a formação de borra na solução.
Como resultado final, a camada de fosfato confere à superfÃcie ótima proteção contra à corrosão, além de excelente aderência da tinta, porém, a sequência operacional é mais longa, com elevado consumo de água.
A revolução dos nanos
Com as diretivas ELV, RoHS, WEEE, cada vez mais se pretende reduzir a utilização de cromo e reduzir os problemas de excesso de consumo de água e energia, além de intensa geração de resÃduos. Assim, novos processos foram desenvolvidos com a introdução da nanotecnologia, camadas entre 100 e 300 nanometros, ou como os processos à base de zircônio, titânio e silanos que apresentaram resultados satisfatórios, mas ainda não atingindo a mesma resistência à corrosão obtida através da fosfatização do alumÃnio. Os tratamentos com silano, porém, compostos basicamente de Si, C, O, têm inúmeros estudos e desenvolvimentos com diferentes compostos.
Os silanos são classificados como silanos (-SiH3), bissilanos (-Si2H5), etc... Acabamento mais ecológico do que os processos de fosfato, com menor geração de resÃduos, menor consumo de energia e de água, contudo, mais sensÃvel à qualidade da água, sendo necessário a utilização de água D.I.
Os da primeira geração tinham como base apenas uma aderência fÃsica do depósito. Com a evolução, os de segunda geração agregam a aderência quÃmica da camada de silano com a superfÃcie do alumÃnio em uma ligação Al-O-Si, continuando a formação da camada com a interligação do silÃcio na forma Si-O-Si. Segundo OOIJ, W.J., 2002 (6), a interligação do filme formado a partir de compostos com bissilanos (Figura 1) resultam em ligações mais fechadas do que aquelas com silanos (Figura 2).
A última geração
[gallery columns="2" size="full" ids="6826,6825"]Muitos estudos foram feitos com os metais do grupo IIIB, IVB e VB da tabela periódica, obtendo os melhores resultados com viabilidade econômica com o zircônio e titânio que podem estar em fórmulas de conversão de camada, individualmente ou combinados. Os produtos para essa aplicação, além desse metal, incluem uma fonte de flúor livre e uma fonte de flúor ligada a esses metais. O flúor livre provoca o ataque ao alumÃnio, e provoca a deposição do titânio ou zircônio presente na solução, formando óxidos metálicos de espessura manométrica, protegendo a superfÃcie.
Grandes reduções de custo e respeito ao meio ambiente são conseguidos com esses processos, uma vez que os consumos de materiais são pequenos, assim como baixo consumo de água e de energia elétrica, com processos mais rápidos e sequências de operação muito mais curtas. Entretanto, a aderência da pintura ainda deixa a desejar. Para melhorar esta deficiência foram introduzidos processos contendo ácidos acrÃlicos e acrilatos, que selam o depósito oferecendo melhoria, mas não tanto quanto o processo de fosfato.
Na geração mais atualizada, são utilizados ácidos orgânicos acrÃlicos, vinÃlicos e fosfônicos com real incremento na aderência e resistência à corrosão, mantendo o mesmo mecanismo de reação dos processos base hexafluorzircônio, porém, completado pela polimerização desses ácidos orgânicos, com melhor selagem da camada depositada, conferindo excelentes resultados de aderência e resistência à corrosão, com todos os benefÃcios da sequência mais curta, podendo ser restrita a apenas 3 ou 4 passos, incluindo as águas de enxágue, possibilitando a utilização com ou sem enxágue final, um processo muito menos sensÃvel à qualidade da água. Não altera o mecanismo de reação do processo de camada de conversão e opera em muito baixa concentração, minimizando o custo do processo.
Esses compostos se concentram na superfÃcie de conversão, exatamente onde interagem, melhorando a resistência à corrosão e a aderência da tinta.
Conclusão
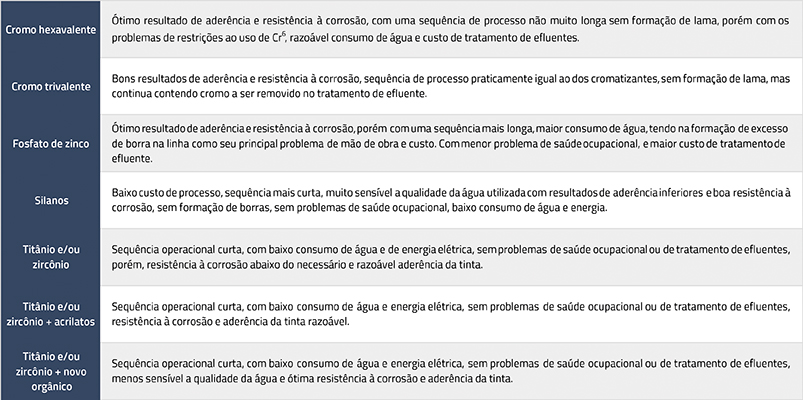
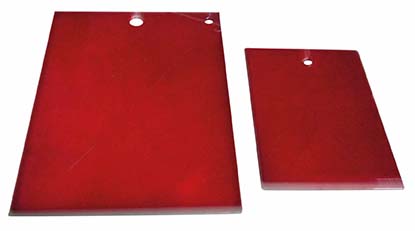
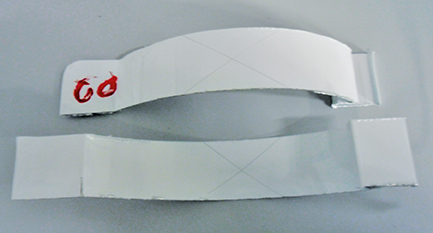
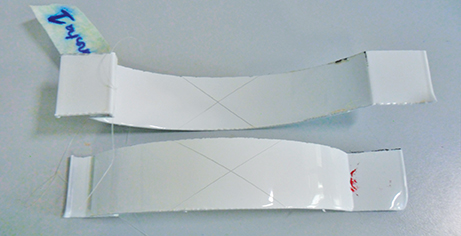
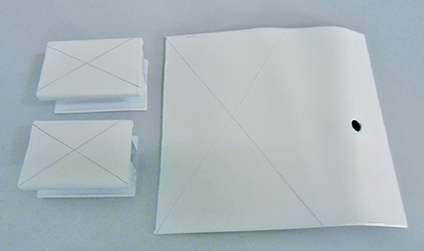
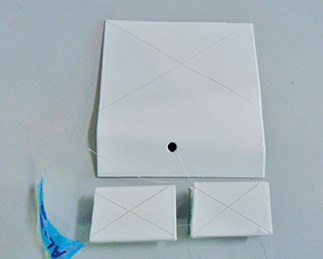
Bibliografia
1. Zinc phosphating solution of aluminium and aluminion alloy – Patent CN101812682A.
2. Chromium compounds – advantages and application Q.Ashton Acton, PhD – General editor.
3. Zirconium pretreatment compositions containing a rare earth metal, associated methods for treating metal substrates, and related metal substrates Nathan J. Silvernail – Mark W. Macmillen – Shan Cheng Patent WO2013019303A1.
4. Pretreatment for aluminium and aluminium alloy – Craig A Matzdorf, California, MD (US); James L. Green, III, Lusby, MD (US); Michael J. Kane, Callaway, MD. (US) patente US 6,521,029 B1.
5. Formation of Zinc phosphate coating on aluminium alloy. Wai honong Kok – B.Sc. – University of Malaya 1977.
6. 6-OOIJ,W.J. Van et. Al, Potential of silanes for chromate replacement in metal finish industries, Ohio, 2002 – University of Cincinnati.