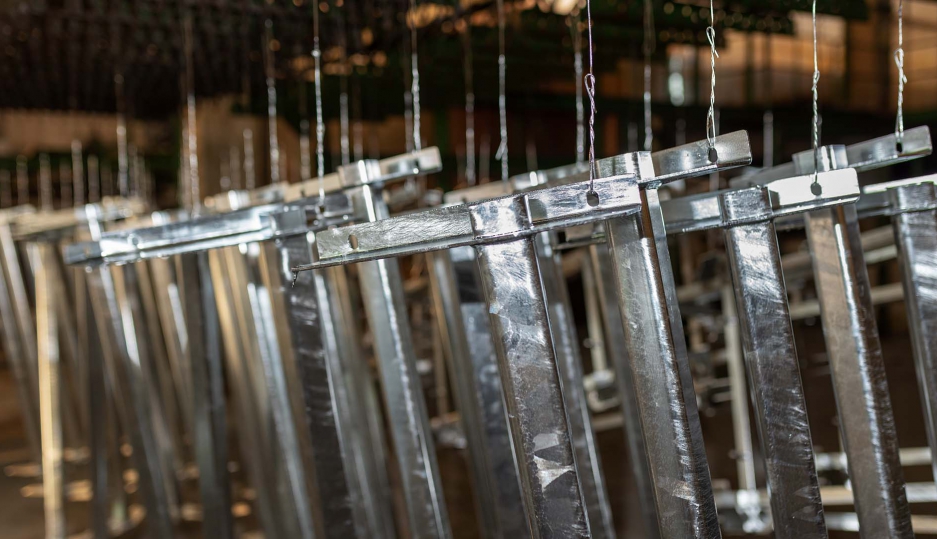
Conheça um dos principais parâmetros para se obter uma melhor qualidade do produto galvanizado e ainda reduzir o consumo de zinco
Engenheira de Desenvolvimento de Produto e Assistência Técnica da Nexa Resources
mariana.souza@nexaresources.com
A galvanização por imersão a quente, também conhecida como zincagem a fogo, é uma das técnicas de proteção contra corrosão mais antigas e efetivas do mercado. Esse processo consiste no revestimento de peças de aço ou ferro fundido em um banho de zinco.
Para que ocorra a reação metalúrgica entre o aço e o zinco, e se obtenha um revestimento uniforme, a superfície da peça deve ser previamente limpa. Assim, o processo de galvanização engloba uma sequência de etapas anterior à etapa de imersão no zinco fundido, conhecidas como etapas de pré-tratamento, conforme ilustrado na Figura 1.
Figura 1. Etapas do processo convencional de galvanização por imersão a quente.
Todas as etapas do processo têm um objetivo específico para assegurar a aderência do zinco à peça e garantir a qualidade final do produto galvanizado. Dentre essas etapas, a fluxagem atua no aumento da molhabilidade da superfície do aço no zinco por meio da remoção da camada de óxido de zinco sobrenadante no banho, como também na dissolução dos óxidos de ferro da superfície da peça que não foram removidos na etapa de decapagem. Além disso, o fluxo protege temporariamente a superfície da peça durante a transferência para a etapa seguinte, evitando assim, que a mesma não entre em contato com a atmosfera e sofra oxidação. .
A fluxagem é uma etapa muito importante por impactar diretamente na qualidade do aspecto superficial da peça como também, no consumo de zinco e geração de resíduos. No entanto, podem surgir algumas dúvidas no galvanizador devido às diferenças dos tipos e formas de preparação desse banho.
Tipos de fluxagem
Com relação aos tipos, existem a fluxagem por método úmido e a fluxagem por método seco, respectivamente em inglês, ‘wet galvanizing’ e ‘dry galvanizing’.
O método úmido consiste na retirada da peça do tanque de enxágue pós-decapagem e imersão direta no banho de zinco fundido, o qual tem um colchão de fluxo sólido e glicerina sobrenadante na superfície do banho de zinco. Como o fluxo é composto por cloreto de amônio, uma substância instável, ele reage com o zinco formando o composto cloreto zinco/amônio.
Já o método seco consiste na retirada da peça do tanque de enxágue pós-decapagem e sua posterior imersão em um tanque de solução aquosa de fluxo, seguido de uma estufa para evaporação dos líquidos e, por fim, a imersão no banho de zinco fundido.
Com base na literatura, a eficiência do fluxo é determinada pela sua ação solvente sob o óxido de ferro, que está totalmente ligada à quantidade de ácido clorídrico liberado. Sendo assim, o método seco, predominantemente utilizado, é uma evolução do método úmido, pois tende a liberar uma maior quantidade desse ácido, proveniente tanto da decomposição do cloreto de amônio, como também da reação com a água.
Formas de preparação e reações químicas
Com relação às formas de preparação, a principal dúvida é no método seco em relação ao fluxo, quantidades e proporções de sais. No método seco, o banho é composto por uma solução aquosa de sais: cloreto de zinco e cloreto de amônio.
Dependendo da proporção entre esses dois sais, o banho pode ser denominado de sal duplo ou sal triplo.
O sal duplo é composto pela proporção de peso molar de 1 parte de cloreto de zinco para 2 partes de cloreto de amônio (1:2), e o sal triplo é composto por 1 parte de cloreto de zinco para 3 partes de cloreto de amônio (1:3). Essa proporção é calculada em massa .
Diante dessa proporção, é possível calcular a razão em massa molar do fluxo:
Para se ter um melhor entendimento sobre como a solução desses sais atua no arraste dos óxidos e sais de ferro presentes na superfície da peça, é importante saber as reações que ocorrem nessa etapa. Assim, os sais cloreto de zinco e cloreto de amônio – sendo este último um composto molecular com dois dipolos NH3 e HCl – reagem formando o composto ZnCl2.NH3 e ácido clorídrico, conforme demonstrado abaixo:
ZnCl2 + NH3.HCl = ZnCl2.NH3 + HCl
À medida que essa solução é aquecida, o composto ZnCl2.NH3 se decompõe em amônia e cloreto de zinco . A adição de cloreto de zinco tem a função de manter o equilíbrio da reação, restringindo o consumo de ácido clorídrico.
O ácido clorídrico irá reagir com os óxidos de ferro e também com o óxido de zinco. A reação do cloreto de amônio com o óxido de zinco da superfície do banho é uma reação exotérmica. Os produtos dessa reação são:
ZnO + 2 (NH3.HCl) = ZnCl2.NH3 + H20 +NH3
Dessa maneira, fazendo uma análise das reações químicas que ocorrem após a imersão da peça no banho de fluxo, é possível concluir que quanto maior a concentração de cloreto de amônio, maior será a reatividade das reações, consequentemente maior arraste dos óxidos e sais presentes no meio.
No entanto, além do fluxo dissolver o óxido de zinco por meio da reação com o ácido clorídrico, ele também pode atacar a peça de aço, pois, como já mencionado anteriormente, a eficiência do fluxo está atrelada a quantidade de ácido clorídrico liberado.
Assim, esse ataque é diretamente proporcional à concentração de cloreto de amônio, ou seja, quanto maior a quantidade de cloreto de amônio do fluxo, maior será a quantidade de cloretos de ferro. Esses cloretos de ferro se dissociam e o ferro livre reage com o zinco, gerando a borra .
Diante disso, a escolha do uso do sal triplo, apesar de proporcionar um aumento na reatividade do fluxo, requer um maior controle de processo, pois caso esse controle não seja efetivo, poderá ocasionar uma maior geração de borra e, consequentemente, um maior consumo de zinco.
Conclusão
Nos Estados Unidos é mais comum o uso do sal triplo e na Europa, como no Brasil, é mais comum o uso do sal duplo. Independentemente da escolha do galvanizador, o importante é ter um bom controle de fluxo; manter as concentrações recomendadas, de 400 a 600 g/l, de sal duplo, e 300 a 400 g/l, de sal triplo; manter o fluxo aquecido em um intervalo de temperatura entre 40 e 70°C; e controlar a acidez do banho (pH = 3 - 4,5) .
Com o controle de todos esses parâmetros é possível obter uma melhor qualidade do produto galvanizado e uma redução do consumo de zinco.
REFERÊNCIAS BIBLIOGRÁFICAS
General Galvanizers Practice, 1965, Part 2 Pretreatment of work for galvanizing, West Midlands: Galvanizers Association, 1999.
INTERNATIONAL CONFERENCE ON HOT DIP GALVANZING, 1., 1950, Copenhagen. Fundamental Aspects of Hot Dip Galvanizing, Oxford: Zinc Development Association, 1951. 22-25 p.
FOSSA, Alana. Flux Quality: Concentration, Density (Baume), Flux Ratio, pH. American Galvanizers Association, 2017
Disponível em: https://galvanizeit.org/knowledgebase/article/flux-quality-concentration-density-baume-flux-ratio-ph. Acesso em: 23 de Dezembro de 2019
INTERNATIONAL CONFERENCE ON HOT DIP GALVANZING, 1., 1950, Copenhagen. The Flux Relative Merits of Flux Galvanizing and Dry Galvanizing, Oxford: Zinc Development Association, 1951. 74-81 p.
Acesse o conteúdo original Publicado na revista Tratamento de Superfície, edição 220, página 21-23